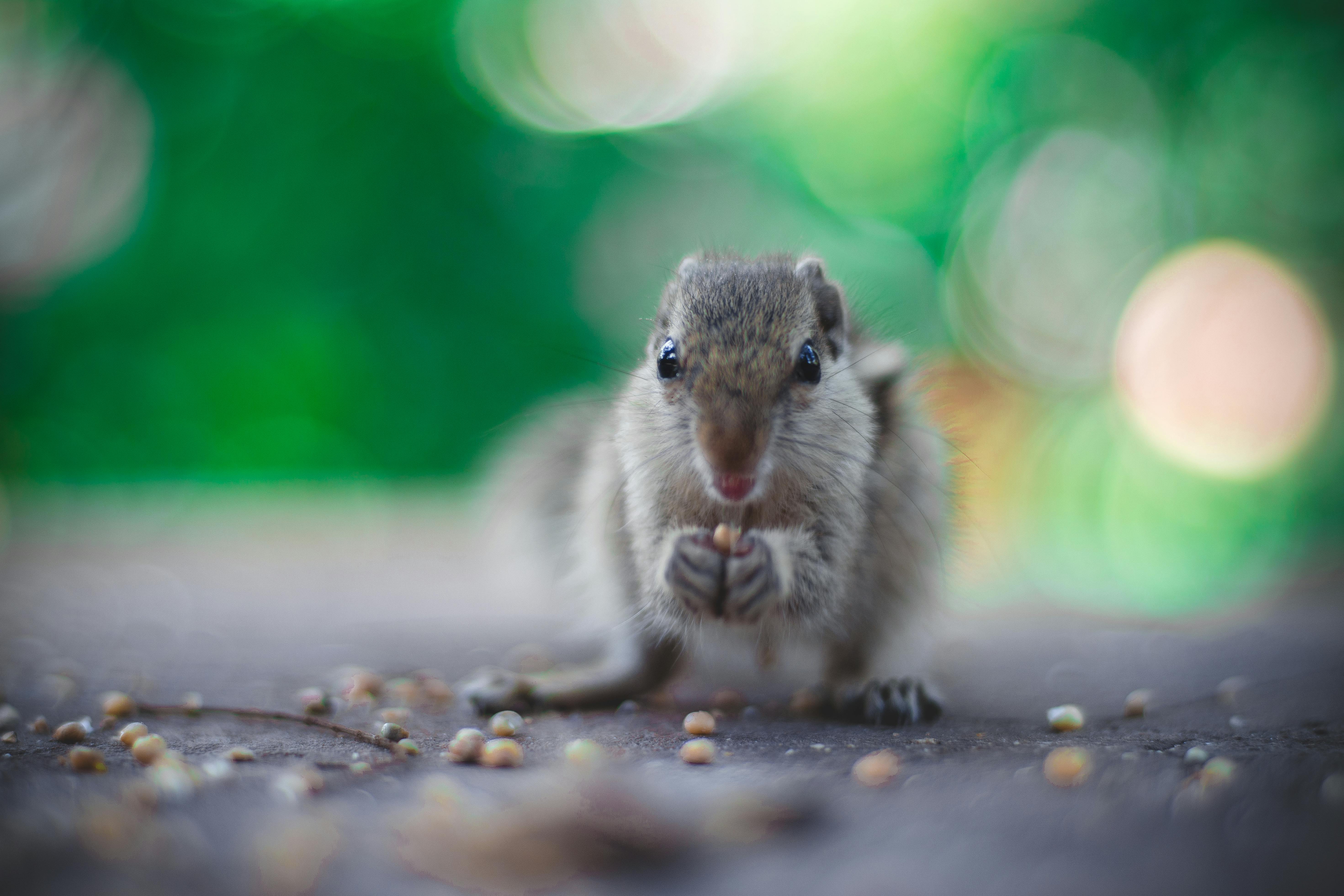
Tank integrity evaluation EEMUA 159 – Non-destructive testing
admin
- 0
The EEMUA 159 inspection is a non-destructive inspection scheme specially oriented to the inspection and maintenance of storage tanks. Regulated bodies and insurance companies often request EEMUA 159 as a quantifiable way to demonstrate that a competent inspection has been carried out.
The EEMUA 159 standard is useful because it encompasses the scope of the inspection, the recognized repair methods, and the inspection and maintenance program in one complete package. This simplifies the maintenance process and helps identify any risk areas quickly and efficiently. EEMUA 159 is done in a risk-based way: inspecting the areas of the tank that are most prone to failure.
The inspection is usually carried out while the tank is out of service, allowing all areas of the tank to be observed. The tank floor is of particular importance as corrosion on the top and bottom side can cause thinning and even total loss of the wall without anyone knowing. There have been cases where a tank has spilled product into the environment over a long period of time so slowly that no one noticed. When the leak was finally discovered, it was not known where the lost volume had actually ended up.
A full inspection covers the most important areas of the tank, including:
Tank floor – Completely scanned to identify any areas of corrosion or thinning. Usually an electromagnetic technique such as LFET (Low Frequency Electromagnetic Test) is used. While thickness measurements are taken with UT (Ultrasonic Testing).
Floor-to-shell welding – This is another high-risk area that needs careful inspection. The weld can be verified using MPI (Magnetic Particle Technique), or if the tank floor is lined, ECT (Eddy Current Technique) can be used. ECT is more comprehensive as it can inspect subsurface defects unlike magnetic particle testing, however it takes much more time.
The tank shell: The shell, which makes up the bulk of the tank, is of obvious importance. Generally, thickness measurements are taken using UT (Ultrasonic Test) and a weld sample; generally between the first two rows they are verified using MPI (magnetic particle test).
The roof: forming another large area of the tank, the roof is again inspected by ultrasound.
Other additional items such as attachments and accessories such as ladders, ladders, nozzles, meters and pipes are inspected. A complete visual assessment is also performed critiquing the entire tank and any surrounding apparatus that may affect the integrity of the tanks.
A full report is provided at the end of the inspection that provides records for maintenance and also as evidence for audits and includes details of the full inspection, as well as calculations and recommendations for repair.